I’m nearly done with version 4 (or maybe 5) of my CNC router. Last year, I started building this from parts I had on hand, including unsupported steel rail and linear bearings, red oak, some crappy lead screws and HDPE (aka, Walmart cutting boards.)
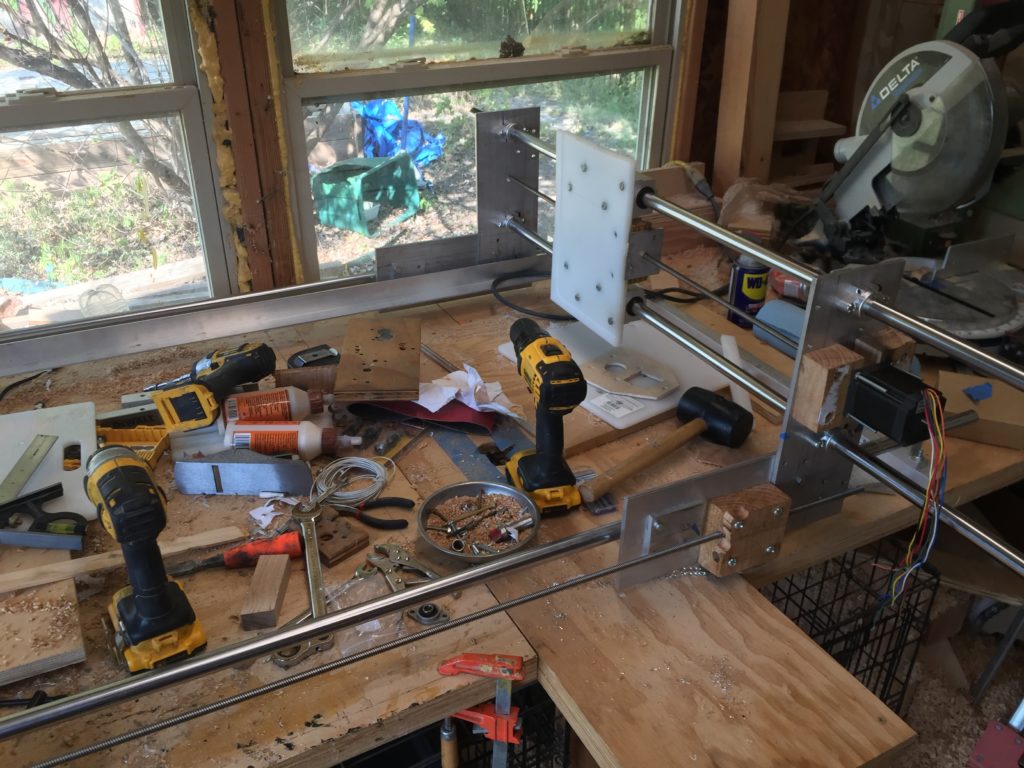
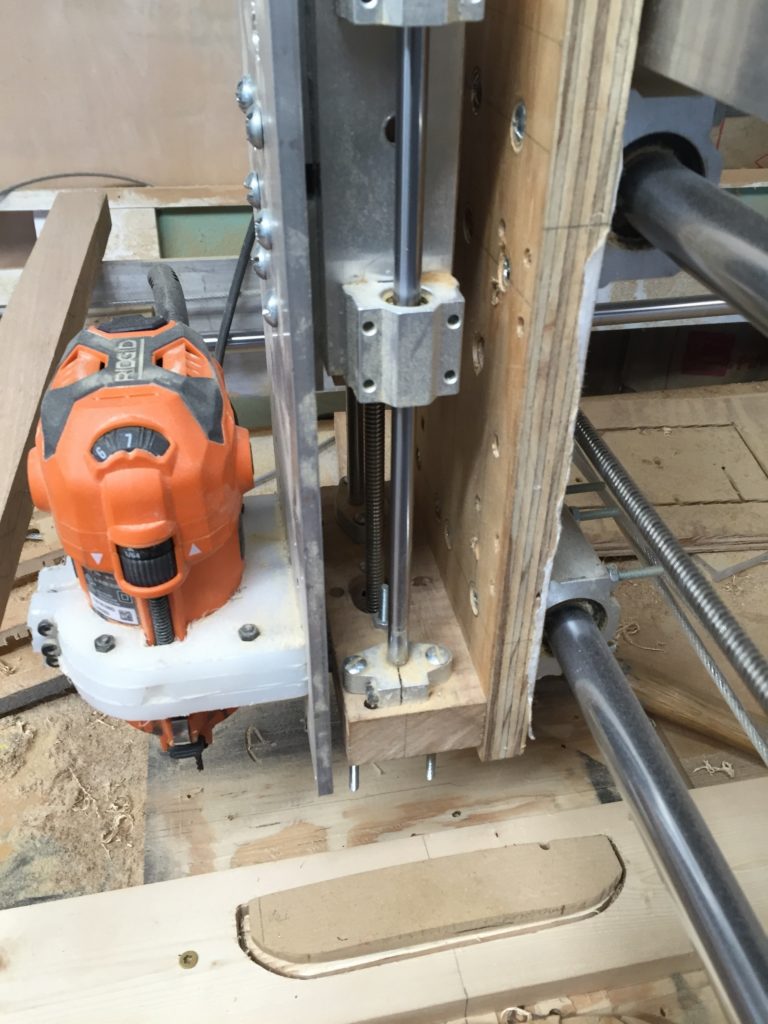
That version mostly worked. But, it wasn’t the most accurate machine.
So, I started replacing wood with 1/2″ aluminum:
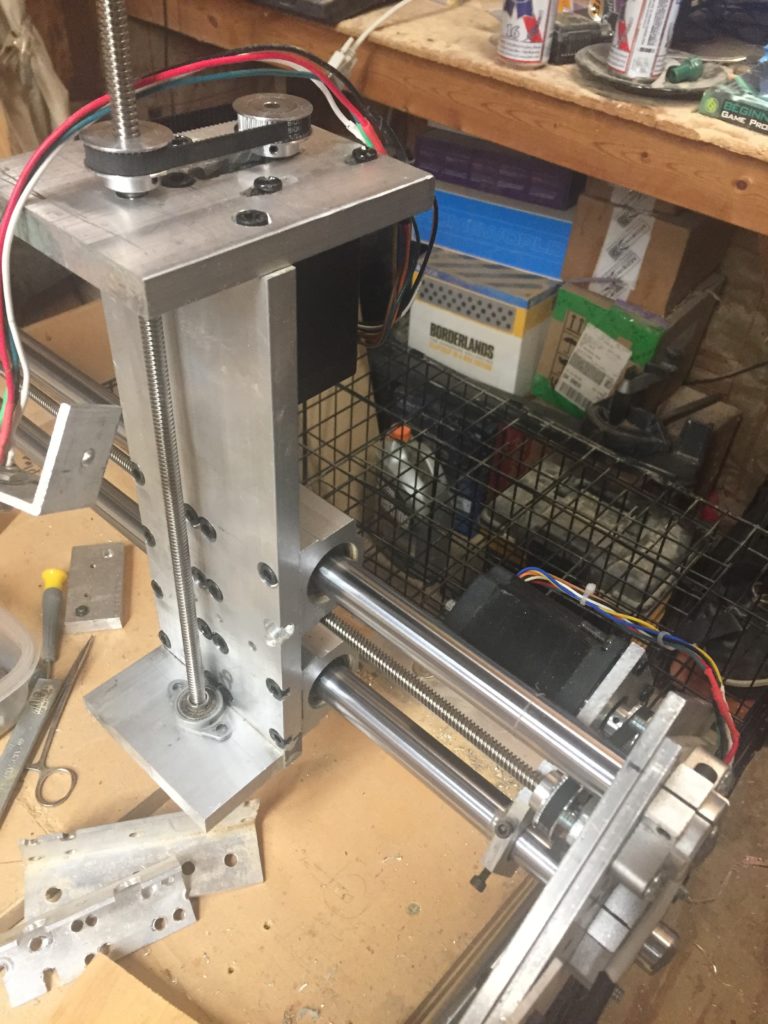
That worked pretty well, but the unsupported rail had a LOT of deflection. I could easily twist the two rails over an inch in the middle of the 38″ span, which is not sufficiently rigid when cutting hardwood.
I had to decide then between different linear motion systems, including fully supported rail, flat carriages, or wheels. I went with OpenBuilds c-beam aluminum extrusion and hard Delrin wheels. I was initially skeptical about the wheels as I suspected they might compress under load. However, so far they’re pretty awesome.
I made custom plates for the carriages and motor mounts and went with a belt drive the long (49″) axis. The short axes use T8 ACME trapezoidal lead screws with Delrin antibacklash nuts.
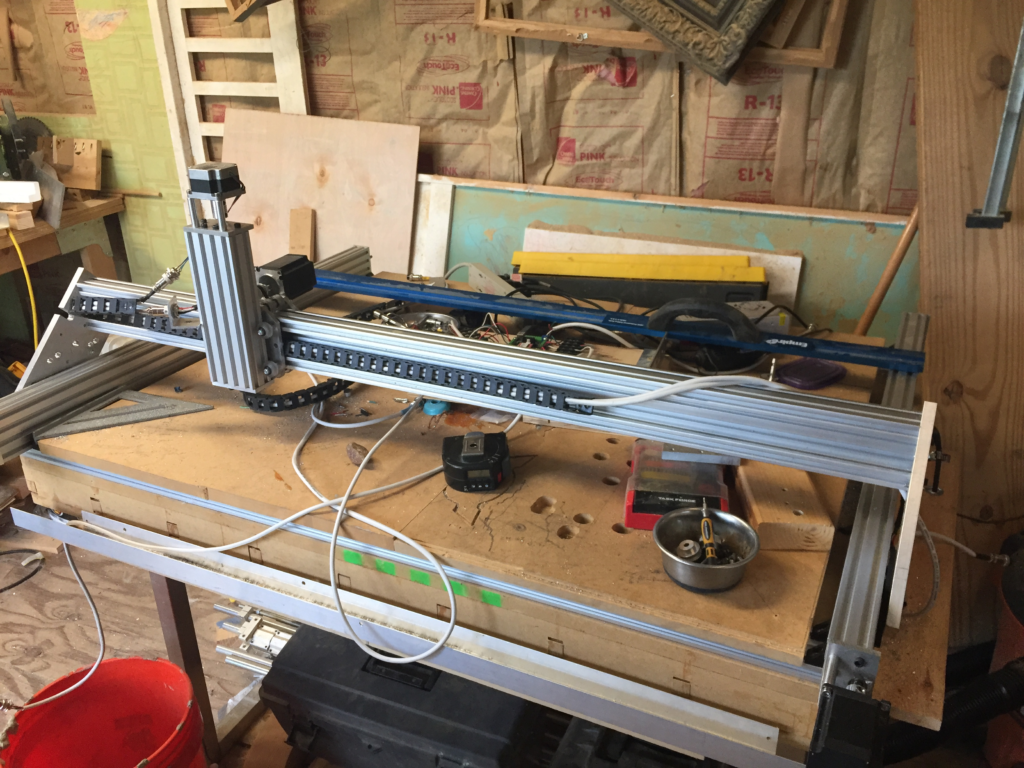
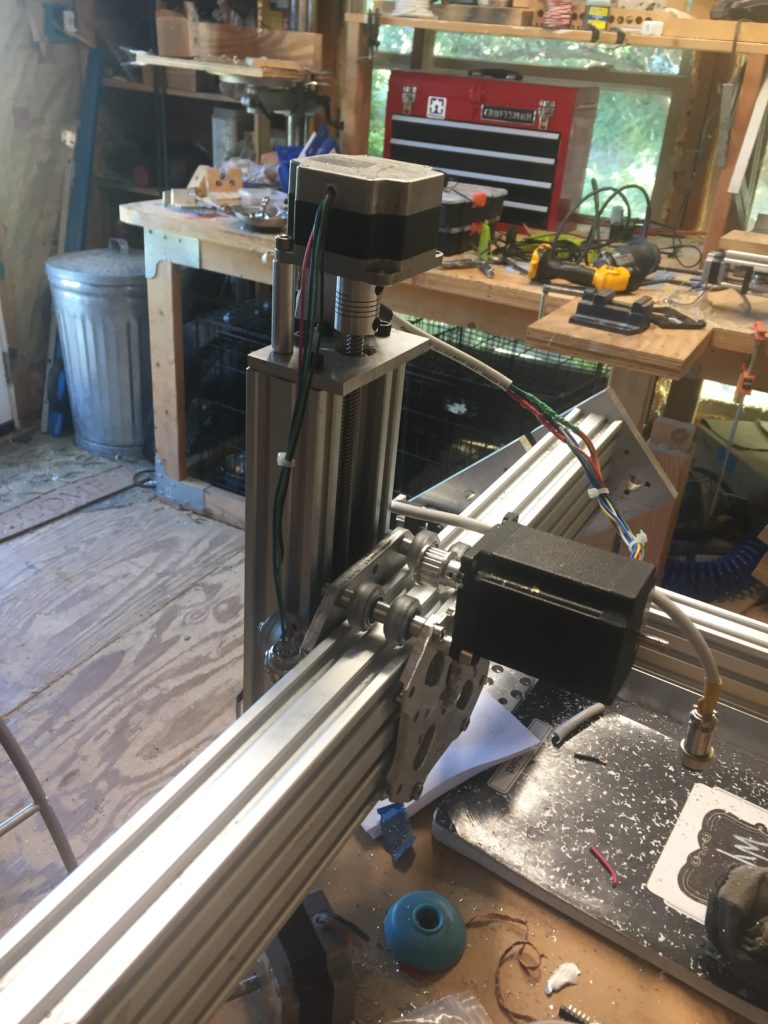
I used my OpenBuilds minimill to make all of the end plates and carriage plates from 1/4″ 6061 aluminum. I broke at least five endmills before switching to a 1/4 router bit. That worked significantly better, but due to the nature of router bits, I could only take off about 0.25mm per pass. It took a little over 30 minutes to cut each of the large carriage plates. But, it’s worth it.
The belt drive is (unsurprisingly) very fast, and so far is accurate and rigid enough for my purposes. Next up: cable routing and dust collection. Depending on how the accuracy tests go, I may need to add some sort of gear reduction system to the belt-driven axis.
Fun, fun, fun! I wonder if this is what it was like to have an erector set as a kid.